Choosing the Right Chlorine Injection Pump for Your System
Chlorine is a keystone of water treatment. Whether you’re maintaining secondary disinfection in a commercial building, controlling biological growth in a cooling tower, or treating well water for microbial safety, chlorine-based systems are relied on for their consistency and effectiveness. But no matter the application, proper delivery is critical — and that, in part, depends on the injection pump chosen by your facility staff or water treatment company.
At EAI, we support facilities across the western U.S. with disinfection strategies built for performance, safety, and operational continuity through sustainable practices. One often-overlooked detail in system design is the chlorine injection pump. Hence, this guide will walk you through the key considerations in choosing the right chlorine injection system — from chemical compatibility and flow rate to control methods and application fit.
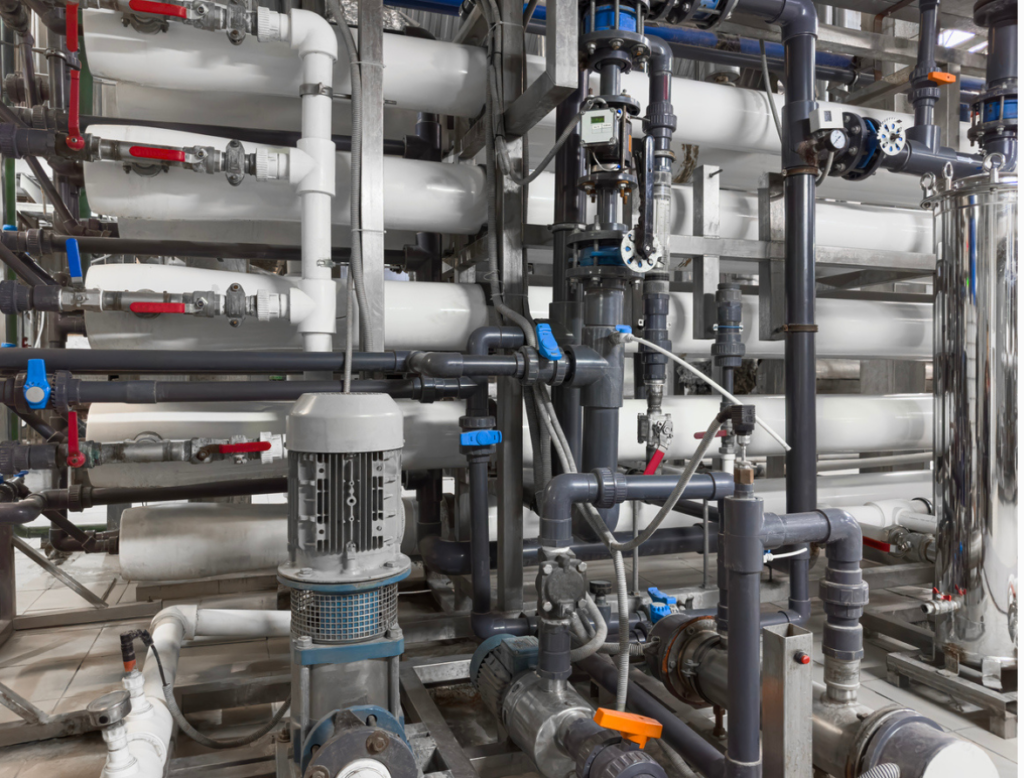
Understanding Chlorine Injection: What It Does and Where It’s Used
Before we get into selection criteria, it helps to understand how chlorine injection functions within various applications of your water treatment system and why various applications call for different approaches.
How Chlorine Injection Works
Most chlorine injection systems rely on sodium hypochlorite (NaOCl) — a liquid form of chlorine commonly known as bleach. A chemical metering pump introduces a precise amount of this solution into a water line, either continuously or in response to flow changes. This process provides reliable disinfection and clean water, oxidizes unwanted compounds like iron and manganese, and helps maintain a safe chlorine residual in the system.
Where Chlorine Injection Pumps Are Used
Well Water Treatment
Chlorine injection is a foundational method for treating well water, especially in systems serving residential communities, schools, or agricultural operations. It serves two key functions: water disinfection and oxidation. Pathogens such as E. coli and Giardia are neutralized effectively, while problematic elements like iron, manganese, and hydrogen sulfide are oxidized and rendered filterable. When integrated with flow-paced controls, chlorine injection pumps can adapt to variable water usage, delivering consistent treatment without overfeeding.
Cooling Towers
In cooling tower systems, microbial control is critical to maintaining heat exchange efficiency and preventing fouling, scaling, and corrosion. Chlorine injection pumps play a vital role by continuously or intermittently feeding sodium hypochlorite into the recirculating water, disrupting the growth of bacteria, algae, and biofilm. Without proper disinfection, microbial buildup can reduce thermal efficiency, damage surfaces, and even contribute to Legionella risk. Injection pumps in these applications often work in coordination with ORP sensors, timers, or building automation systems to ensure accurate dosing parameters under dynamic load conditions.
Secondary Disinfection in Building Plumbing
Large commercial buildings, hospitals, and multifamily residences increasingly rely on secondary disinfection to reduce risks associated with Legionella and other waterborne pathogens. In these facilities, chlorine injection systems maintain a consistent disinfectant residual throughout the plumbing distribution network. Chemical injection pumps are often installed downstream of central storage tanks or near critical system entry points to boost chlorine levels as water circulates through complex piping layouts. When paired with real-time monitoring, these pumps can help ensure compliance with ASHRAE 188 and state-level water management guidelines.
Agricultural Irrigation Systems
Biofilm, algae, and organic debris can clog irrigation lines and reduce the effectiveness of drip and micro-irrigation systems. Chlorine injection is commonly used to prevent these issues by maintaining microbial control and keeping lines clean. Dosing pumps are calibrated to the flow of irrigation water, delivering chlorine at levels high enough to disinfect without damaging crops or soil. In some operations, chlorine is also used to oxidize iron and manganese, preventing sediment buildup in emitters. For growers managing thousands of feet of piping or working with reclaimed water, chlorine injection is a practical and cost-effective solution.
Food and Beverage Facilities
Clean-in-place (CIP) systems, process water lines, and sanitation stations in food and beverage facilities depend on chlorine injection to maintain hygienic conditions. Sodium hypochlorite is commonly used to disinfect surfaces, rinse equipment, and treat incoming water supplies. Pumps in these settings must meet strict performance and material standards — often NSF-certified — to avoid cross-contamination and ensure dosing accuracy. Chlorine injection supports regulatory compliance and reduces the risk of spoilage or contamination, especially in high-throughput production environments where downtime is costly.
Wastewater Treatment
In municipal and industrial wastewater treatment needs, chlorine injection is oftentimes used for final disinfection of treated effluent before discharge or reuse. Injection pumps ensure the precise addition of chlorine to meet local environmental and industry regulations while minimizing chemical usage and byproduct formation. Depending on the plant’s design, dosing may occur post-filtration, at the point of discharge, or prior to storage in holding ponds. These systems often rely on advanced monitoring and control schemes to maintain residual targets and ensure safe, compliant operation without operator intervention.
Key Factors to Consider When Choosing a Chlorine Injection Pump
Not all chlorine injection systems are created equal. Selecting the right pump means taking a close look at your system’s flow characteristics, chemical requirements, control needs, and environmental conditions. Here are the critical considerations when choosing a chlorine injection pump for your system:
1. System Flow Rate and Pressure
A chlorine injection pump must be able to deliver the right dose of chemical at the correct rate — no more, no less. This requires matching the pump’s output capacity (usually in gallons per hour or liters per hour) to your system’s flow rate. For example, a small well system may only need a fraction of a gallon per hour, while a large cooling tower loop might demand significantly higher throughput.
It’s also important to account for system pressure, especially if the injection point is downstream of a pressurized line. Pumps that can’t overcome system pressure will struggle to inject consistently, leading to underfeeding or complete feed failure. We often recommend pumps with adjustable stroke rates or variable-speed drives for systems where flow rates fluctuate or ramp up seasonally.
2. Chlorine Type and Chemical Compatibility
The most common chlorine source in these systems is sodium hypochlorite, which is highly effective but also chemically aggressive. It can degrade seals, diaphragms, and tubing that aren’t designed for strong oxidizers. That’s why material compatibility is a must.
Look for pumps constructed with PVDF, PTFE (Teflon), or Viton in wetted parts. Standard plastics like polypropylene or rubber seals may break down over time, leading to leaks or inconsistent feed. If you’re working with stronger or more concentrated solutions, or if your system includes acidic pre-treatment, chemical resistance becomes even more critical.
3. Control Method: Manual, Timed, or Feedback-Based
Your pump should integrate with your system’s operational strategy. There are three main types of control:
- Manual Control: Good for systems with stable, low flow. The operator sets the pump output and adjusts it as needed.
- Timed Control: Uses a timer or relay to pulse the pump on and off — helpful in batch systems or irrigation schedules.
- Flow-Paced or Sensor-Based Control: Ideal for dynamic systems. These pumps adjust dosing automatically based on the readings from flow meters, ORP sensors, or chlorine residual analyzers. They’re commonly used in cooling towers, secondary disinfection, and industrial processes where demand fluctuates.
Choosing the right control strategy is just as important as the pump specs themselves. Our team regularly integrates pumps with building automation systems, SCADA platforms, and remote monitoring tools to provide real-time control and peace of mind.
4. Materials of Construction
We touched on this earlier, but it bears repeating: chlorine is corrosive, especially over time. Choosing the right materials for pump heads, valves, seals, and tubing can significantly extend equipment life and reduce maintenance.
Recommended materials for chlorine service include:
- Pump heads: PVDF or ceramic
- Seals and diaphragms: Viton, EPDM, or PTFE
- Tubing and injection quills: Teflon-lined or braided polyethylene
EPDM is suitable primarily for diluted chlorine solutions or lower-concentration applications, while PTFE (Teflon) or Viton are recommended for concentrated or aggressive chlorine applications.
If you’re operating in a high-temperature, UV-exposed, or outdoor environment, material durability becomes even more important. EAI can help specify chlorine injection systems with proper enclosures, sun shielding, or secondary containment as needed.
5. Safety Features and Alarm Integration
Chlorine is effective, but it’s not a chemical to take lightly. The right pump should offer built-in safeguards, especially in sensitive environments like healthcare, food processing, or schools.
Look for features such as:
- Leak detection sensors
- Low-level chemical alarms
- Flow interruption fail-safes
- Remote alarm capabilities
- Secondary containment trays
EAI frequently integrates pumps with broader control systems that alert operators in real time if a problem arises — minimizing chemical exposure risks and supporting rapid response.
Types of Chlorine Injection Pumps
Once you’ve identified your system’s needs — the next step is selecting the right pump type. The precise dosing and accuracy of a pump matters, especially in systems where residual levels are tightly regulated. Look for pumps with turndown ratios that match your system’s variability — the wider the range, the more flexible your control. Chlorine injection pumps come in several configurations, each suited to different applications, operating conditions, and dosing goals. Choosing the correct type can improve dosing accuracy, simplify maintenance, and increase equipment life — all while helping you stay within budget and on target for regulatory compliance.
Below are the most common types of chlorine injection pumps used in water treatment systems, along with the pros and cons of each.
1. Diaphragm Pumps (Mechanically or Solenoid-Driven)
These are the most widely used pumps in industrial applications and commercial water treatment for good reason. Diaphragm pumps use a flexible membrane to draw in and discharge fluid in controlled volumes. The motion is driven either by a motor with a crankshaft (mechanical) or a solenoid coil that pulses the diaphragm (solenoid-driven).
Strengths:
- Highly accurate, repeatable chlorine dosing
- Good for medium to high-pressure systems
- Compatible with aggressive chemicals like sodium hypochlorite
- Available with flow-paced and sensor-based control options
Best Fit For:
Cooling towers, secondary disinfection, well water systems, and any application requiring consistent water flow under pressure. These pumps are reliable workhouses, ideal for systems that operate continuously or require precise metering across varying conditions.
2. Peristaltic Pumps
Also known as hose or tube pumps, peristaltic pumps operate by squeezing a flexible tube in a rotating motion, pushing the chemical through without exposing it to pump internals. Because the fluid only contacts the inner tubing, they’re easy to maintain and less susceptible to corrosion.
Strengths:
- Gentle pumping action — great for gas-forming solutions like sodium hypochlorite
- Simple design with minimal moving parts
- Easier to prime and clean
- Excellent for low-pressure, small-scale systems
Best Fit For:
Irrigation systems, lab-scale applications, low-flow disinfection, or systems with off-grid or intermittent operation. They’re also useful when suction lift is required, such as drawing from a tote or chemical tank below the pump.
3. Piston Pumps
Piston pumps use a reciprocating plunger to inject chemicals under high pressure. While extremely precise, they are typically reserved for systems that demand strong pressure performance or aggressive dosing control, and are less common in standard chlorine injection system.
Strengths:
- Handles high-pressure systems well
- Very accurate and adjustable output
- Long service life in compatible applications
Best Fit For:
Industrial processes requiring high-pressure chemical injection, such as boiler treatment or certain process water systems. Due to their complexity and higher maintenance needs, these are not typically the first choice for chlorine service unless specifically warranted by system design.
4. Solenoid Dosing Pumps
Technically a type of diaphragm pump, solenoid-driven pumps deserve their own mention because of their compact size, electronic control, and affordability. These are often used in light commercial systems and are compatible with automated control inputs like pulse signals or 4–20 mA analog controls.
Strengths:
- Compact and operational cost-effective
- Works well with automation systems
- Simple to install and operate
- Good for precise chlorine dosing in small systems
Best Fit For:
Small-scale chlorine injection systems with variable flow, including small cooling towers, secondary disinfection in commercial buildings, and remote sites where space and simplicity are key. Just be sure to check compatibility with your chemical concentrations and system pressure.
Choosing the Right Fit for Your System
There’s no one-size-fits-all pump. Each system has unique hydraulic conditions, chemical handling requirements, and operational priorities. At EAI, we assess your site conditions, water quality goals, and infrastructure needs before recommending a pump. We also consider long-term cost of ownership — including maintenance intervals, spare part availability, and upgrade potential to ensure you’re investing in a system that performs reliably and adapts as your needs evolve.
EAI’s System-Specific, Customizable Solutions
A chlorine injection system may be a small component in your overall water treatment system but its impact is anything but minor. The right pump ensures that disinfection happens exactly as needed, minimizing chemical wastage, reducing risks, and guesswork. It helps you protect infrastructure, meet compliance standards, and keep your system running at optimal performance day after day.
But choosing the right pump isn’t just about selecting a model number. It’s about understanding your system as a whole — your water chemistry, pressure conditions, flow variability, and disinfection goals — aligning equipment decisions with that bigger picture.
At EAI, we’ve built our reputation on helping clients do just that. Whether you’re managing a critical healthcare facility, a sprawling commercial complex, or a remote well system, our team and cutting edge technology brings decades of field-tested experience, deep technical insight, and a commitment to customizable solutions that last. We don’t just install pumps — we build partnerships that ensure your water treatment program is smart, safe, and sustainable.
Need help choosing the right chlorine injection pump for your system?
Let EAI’s in-house experts walk your site, review your goals, and deliver a system recommendation that fits your operation, your budget, and your long-term plan.
Contact us today to schedule a consultation — and see how the right equipment, backed by the right people, makes all the difference.
Frequently Asked Questions (FAQs)
No — chlorine dioxide is a highly reactive oxidizer and must be generated and dosed using specialized equipment. Standard chlorine injection pumps are not chemically compatible and can degrade quickly or create unsafe conditions. If you’re considering ClO₂, EAI offers onsite generation systems designed specifically for that chemistry.
Accuracy depends on proper calibration and control integration. Pumps paired with flow sensors, ORP probes, or chlorine residual analyzers can adjust dosing in real time. EAI can help you implement or fine-tune monitoring systems to ensure your dosing matches system demand and maintains safe, compliant levels.
Diaphragm pumps are best for pressurized systems and precise, continuous dosing. Peristaltic pumps are better for low-pressure or intermittent applications and are easier to maintain since the chemical only contacts the tubing. The right choice depends on your system’s flow, pressure, and operational rhythm.
Maintenance needs vary based on usage, chemical concentration, and environmental conditions. In general, diaphragms, seals, and tubing should be inspected quarterly. EAI provides maintenance programs and system audits to keep your pump operating reliably and catch small issues before they become costly problems.
Yes. We offer full lifecycle support — from system design and equipment selection to installation, calibration, maintenance, and troubleshooting. Our field service team is equipped to handle on-site support across California, Arizona, Nevada, Utah, and Washington.