Water Quality Monitoring: Key Metrics for Cooling Towers
Monitoring water quality is essential for keeping cooling towers running efficiently and reliably. These systems face challenges like corrosion, scaling, and microbial growth, which can lead to higher operational costs, equipment failures, and health risks such as Legionella outbreaks.
To mitigate these risks, cooling towers must comply with strict regulatory standards, including the Environmental Protection Agency’s (EPA) NPDES requirements and ASHRAE 188 guidelines for Legionella prevention. Effective water management strategies, supported by advanced monitoring technologies, allow facilities to optimize performance, improve water treatment efficiency, and protect the environment.
With over 35 years of expertise, EAI Water helps facilities achieve these goals through tailored solutions, including real-time monitoring tools, low-dose chemical treatments, and proactive maintenance programs. Our approach ensures compliance, reduces costs, and extends equipment lifespan.
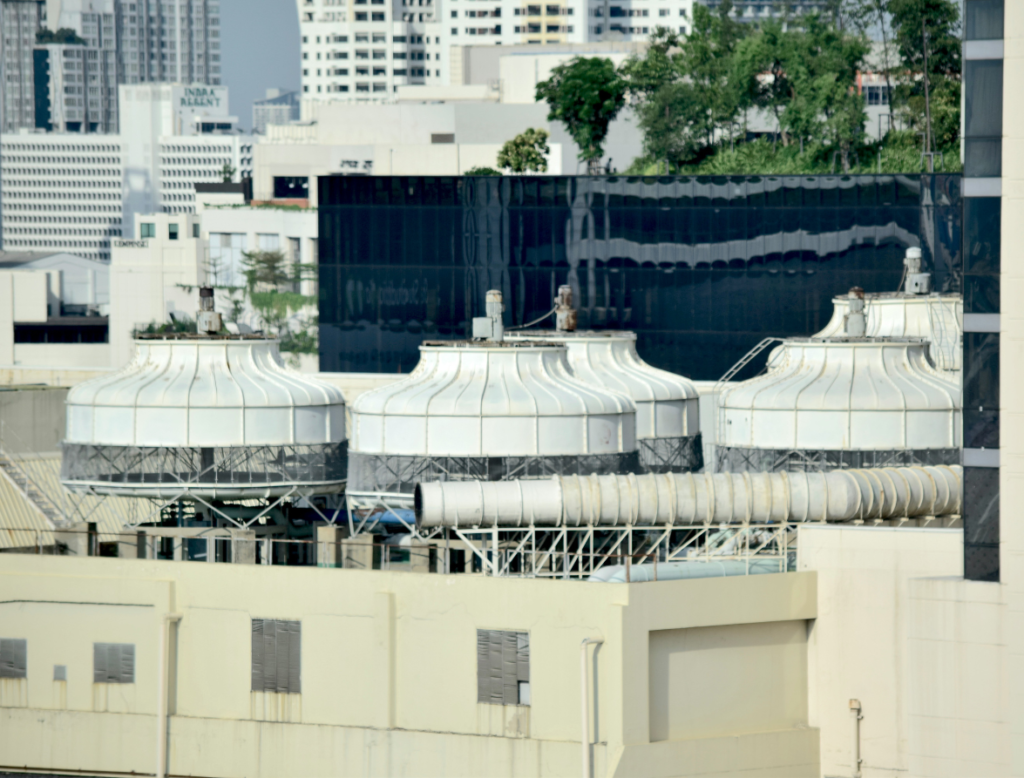
Regulatory Compliance for Cooling Towers
Regulatory standards ensure cooling tower operations remain efficient, safe, and environmentally responsible. Organizations such as the Environmental Protection Agency (EPA) and ASHRAE set guidelines to help facilities manage water quality and minimize risks.
Meeting EPA Standards
The EPA’s National Pollutant Discharge Elimination System (NPDES) outlines requirements for limiting pollutants in cooling tower discharge. Facilities are expected to monitor key parameters, including pH and residual oxidants, to minimize chemical runoff and comply with local permits. Leveraging real-time monitoring tools simplifies compliance while reducing environmental impact.
Managing Legionella Risks with ASHRAE 188
ASHRAE Standard 188 focuses on preventing Legionella outbreaks in water systems, including cooling towers. It emphasizes routine microbial testing and proactive management strategies, such as:
- Periodic testing for biofilms and bacteria.
- Implementing disinfection methods like biocides or UV systems.
- Maintaining records of testing and corrective actions.
By staying aligned with these regulatory frameworks, facilities protect their operations, reduce health risks, and promote sustainable practices.
Monitoring and Testing Details
Effective cooling tower management relies on accurate and consistent monitoring of key water quality parameters. By combining real-time monitoring technologies with periodic testing, facilities can identify potential issues early and take corrective action to maintain system performance and compliance.
Advanced Monitoring Techniques
Modern tools provide precise, real-time insights into water quality and help streamline operations. Recommended technologies include:
- Turbidity Sensors: Measure water clarity to detect suspended particles and biofilm precursors.
- Total Organic Carbon (TOC) Analyzers: Track organic material that can fuel microbial growth and biofilm formation.
- Conductivity Meters: Monitor dissolved solids to ensure proper blowdown and reduce scaling risks.
Continuous vs. Periodic Testing
- Continuous Monitoring: Real-time sensors continuously track parameters like conductivity, pH, and oxidant levels, enabling automated dosing and immediate adjustments.
- Periodic Testing: Routine water sampling for microbial activity, alkalinity, and hardness complements real-time data, providing a comprehensive view of system health.
Key Water Quality Parameters
- pH: Maintain a balanced range (6.5–8.5) to prevent scaling or corrosive conditions.
- Microbial Activity: Regular tests for Legionella and biofilm formation are critical for health and safety.
- Hardness and Alkalinity: Manage these factors to reduce scaling and optimize system efficiency.
Microbial Control in Cooling Towers
Controlling microbial activity is critical to maintaining safe and efficient cooling tower operations. Left unchecked, microorganisms can lead to biofilm formation, reduced heat transfer efficiency, and serious health risks such as Legionella outbreaks. While chemical biocides are a common solution, integrating alternative or complementary disinfection methods can further enhance microbial control.
Chemical Biocides
- Oxidizing Biocides: Chlorine dioxide and bromine are highly effective in eliminating bacteria, viruses, and algae. These are typically used in routine disinfection to control microbial growth.
- Non-Oxidizing Biocides: Used periodically to target resistant microorganisms, these biocides disrupt the cell structures of biofilms for thorough cleaning.
Alternative Disinfection Methods
- UV Treatment: Ultraviolet systems neutralize microbial DNA, preventing replication without the use of chemicals. This eco-friendly method works well for systems aiming to reduce chemical reliance.
- Advanced Oxidation Processes (AOPs): AOPs generate highly reactive hydroxyl radicals, which degrade organic matter and biofilms effectively. This method is particularly beneficial for minimizing biofilm formation in high-risk areas.
- Ozone Treatment: Ozone provides powerful disinfection with minimal residuals, aligning with sustainability goals and reducing the environmental impact.
Proactive Microbial Monitoring
Incorporating advanced microbial monitoring tools, such as ATP meters and online biofilm sensors, helps facilities:
- Detect early-stage microbial growth.
- Assess the effectiveness of biocides and alternative treatments.
- Optimize disinfection practices to meet compliance standards like ASHRAE 188.
Combining chemical and non-chemical approaches ensures comprehensive microbial control, reducing health risks and extending system performance.
Environmental Considerations for Cooling Tower Water Treatment
Effective cooling tower water management not only improves operational efficiency but also plays a crucial role in reducing environmental impact. Facilities can align with EPA’s sustainability goals and support environmental protection through strategic water treatment practices.
Reducing Chemical Discharge
Excessive chemical use in cooling towers can lead to harmful discharges into the environment. By implementing:
- Low-Dose Chemical Treatments: Custom formulations minimize chemical usage while maintaining water quality.
- Optimized Blowdown Practices: Conductivity-based blowdown reduces unnecessary water and chemical waste.
- Real-Time Monitoring: Continuous monitoring ensures precise dosing, avoiding overuse of biocides or inhibitors.
Minimizing Water Waste
Cooling towers are among the largest consumers of water in industrial systems. Facilities can lower their water footprint by:
- Increasing cycles of concentration through improved pretreatment, such as reverse osmosis or dealkalization.
- Recovering and reusing water from blowdown, which reduces the demand for fresh water.
- Reducing evaporation losses by optimizing cooling tower efficiency.
Sustainable Disinfection Practices
Switching to environmentally friendly disinfection methods like UV treatment or ozone systems helps facilities meet regulatory standards while minimizing chemical residuals in discharge water. These methods are especially useful for facilities located in areas with strict environmental regulations.
Meeting EPA Compliance
By adopting water treatment strategies that prioritize sustainability, facilities can ensure compliance with the EPA’s NPDES requirements. These strategies not only protect the environment but also reduce long-term operating costs.
Corrosion and Scaling Prevention
Corrosion and scaling are two of the most common challenges in cooling tower operations, both of which can significantly reduce efficiency, increase maintenance costs, and shorten equipment lifespan. By monitoring water chemistry and implementing preventative strategies, facilities can protect their cooling systems and ensure long-term reliability.
Corrosion Prevention
Corrosion occurs when metal components react with dissolved oxygen, chlorides, or other corrosive agents in the water. Preventative measures include:
- Corrosion Inhibitors: Chemicals such as molybdates, phosphates, and azoles form protective films on metal surfaces, reducing corrosion rates.
- Oxygen Scavengers: These reduce dissolved oxygen levels, which are a primary driver of corrosion in cooling tower systems.
- Material Compatibility: Using corrosion-resistant materials, such as stainless steel or composite components, can mitigate damage in high-risk areas.
Scaling Prevention
Scaling results from the precipitation of dissolved minerals like calcium carbonate, which accumulate on heat exchange surfaces and reduce efficiency. Key strategies for prevention include:
- Conductivity Monitoring: Regularly monitoring conductivity levels ensures dissolved solids remain within acceptable limits, guiding blowdown frequency and reducing scaling risks.
- Scale Inhibitors: Phosphonates and polymers are effective at keeping scale-forming minerals in solution, preventing their deposition on critical surfaces.
- Pretreatment Systems: Technologies like reverse osmosis (RO) or water softeners remove hardness from feedwater, minimizing scaling potential.
Real-World Impact
Case studies have shown that facilities using continuous monitoring and proactive water chemistry adjustments have significantly reduced corrosion and scaling rates. For example:
- A manufacturing facility reduced equipment downtime by 30% after implementing automated monitoring systems.
- Adjusting conductivity settings and chemical dosages led to a 25% decrease in maintenance costs at a commercial cooling tower site.
By combining advanced monitoring tools with tailored chemical treatments, facilities can achieve optimal cooling tower performance while minimizing costly damage.
Take Control of Your Cooling Tower Water Quality
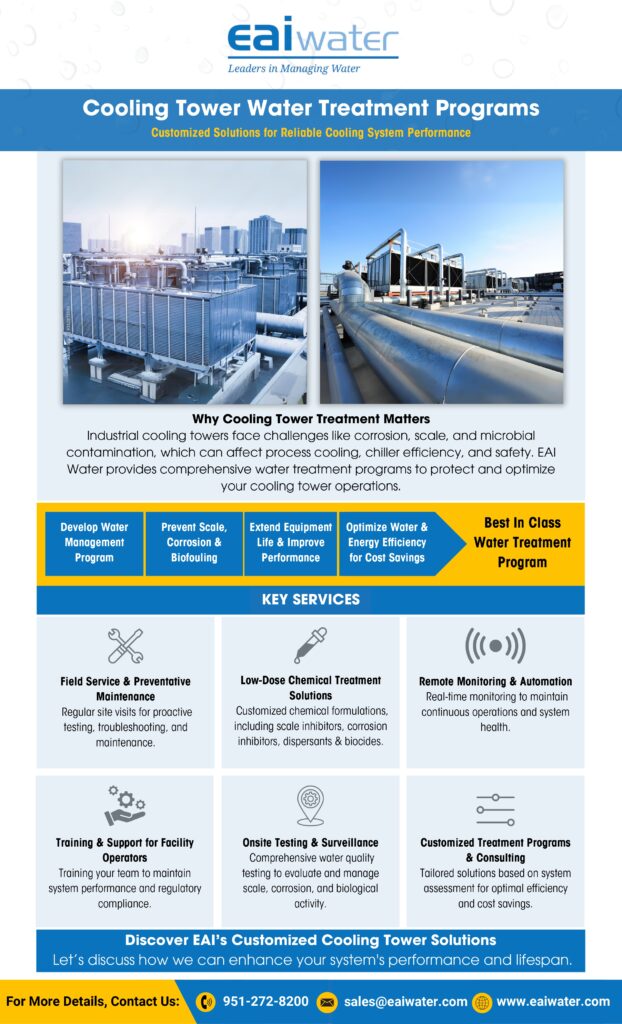
Cooling tower water management is about more than just maintaining operational efficiency—it’s about protecting your equipment, reducing costs, and supporting sustainability. At EAI Water, we provide tailored solutions designed to address your facility’s unique challenges, ensuring compliance with regulatory standards like the EPA’s NPDES requirements and ASHRAE 188.
With over 35 years of expertise, we combine advanced monitoring technologies, low-dose chemical treatments, and proactive maintenance programs to deliver measurable results. From reducing corrosion and scaling to improving microbial control, our strategies help facilities extend equipment life and optimize performance.
Ready to improve your cooling tower water quality? Learn more about our solutions or contact us to schedule a free onsite consultation with our experts.
FAQs
Q: How often should cooling tower water quality be tested?
A: Testing frequency depends on your system and operational demands. However, most facilities benefit from weekly testing for key metrics like pH, conductivity, and microbial activity.
Q: What are the benefits of using low-dose chemical treatments?
A: Low-dose treatments reduce environmental impact, save costs, and enhance efficiency by maximizing cycles of concentration and minimizing chemical waste.
Q: How can remote monitoring improve system reliability?
A: Remote monitoring provides real-time data on water quality and system performance, enabling automated dosing and quick responses to potential issues, preventing costly downtime.
Q: Why is Legionella testing important for cooling towers?
A: Cooling towers provide ideal conditions for Legionella growth, which can lead to health risks. Regular testing ensures compliance with safety standards and protects against outbreaks.
Q: What sets EAI apart in cooling tower water treatment?
A: EAI offers customized solutions that combine advanced monitoring technology, low-dose chemicals, and preventative maintenance. Our programs are designed to reduce water use, lower energy costs, and extend equipment lifespan.