The Role of Pre-Treatment in Maximizing Reverse Osmosis System Longevity and Efficiency
Reverse osmosis (RO) membranes are susceptible to fouling and scaling when systems are not designed properly or when feed water conditions are not altered in a way to protect the treatment system. One common downfall of reverse osmosis systems is when particulates, biological matter, and mineral scale build up on membrane surfaces, reducing separation efficiency and flux. As a result, proper pre-treatment of feed water into a reverse osmosis system is crucial to maximizing system performance and longevity.
Implementing an effective pre-treatment process protects sensitive RO membranes by removing or neutralizing contaminants that could negatively impact membrane health. Doing so maintains steady system operation, production quality, and reduces the need for frequent cleanings. In addition, pre-treatment optimizes RO recovery rates and water usage efficiency. This article will explore key aspects of RO pre-treatment, best practices for optimization, and consequences of insufficient pre-treatment. Proper system design and operation hinges on adequate front-end treatment.
Understanding RO System Challenges
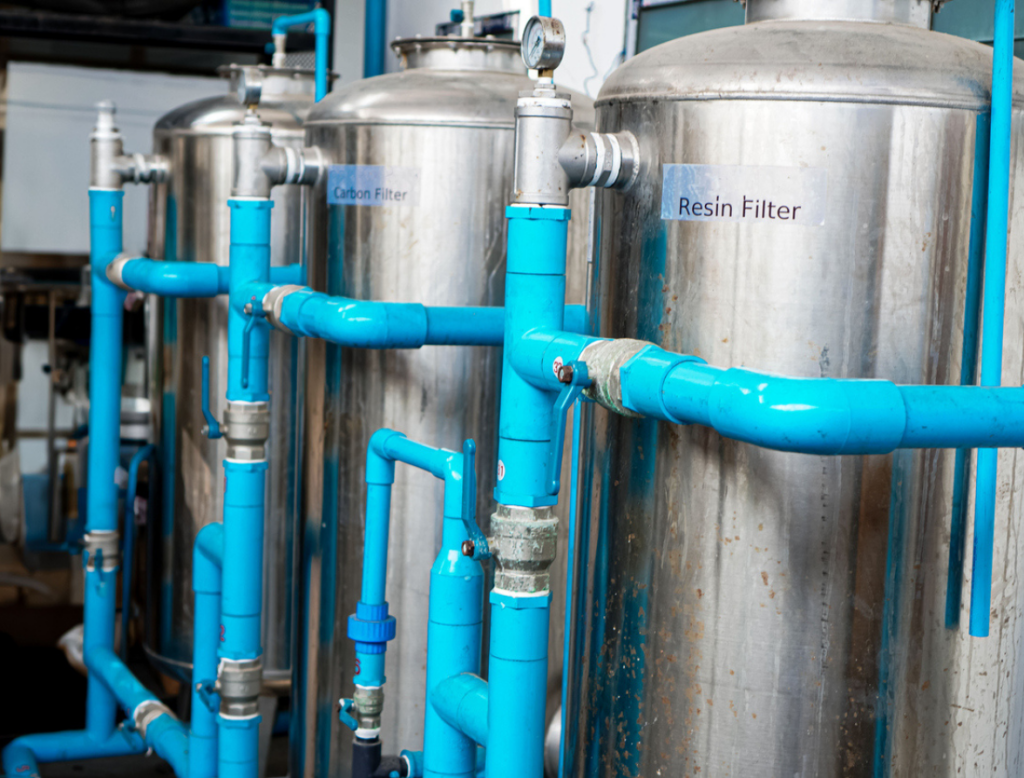
RO systems face several common challenges that jeopardize performance and membrane lifespan if not adequately addressed. Key issues include:
Fouling
Particulates, microorganisms, and organic matter can attach to the membrane surface over time. This fouling layer increases resistance to permeate flow, requiring higher operating pressures and energy costs. In this scenario, flux rates steadily decline as fouling accumulates, reducing permeate (clean water) production.
Scaling
Soluble minerals like calcium carbonate and silica can precipitate on the membrane surface if saturation levels are exceeded. Scaling can occur faster at higher recovery rates due to the concentration of these minersal in the feedwater stream. Mineral scale, when present, compresses and damages the membrane fibers and can lead to membrane replacement.
Chemical Attack
Oxidizing agents like chlorine, if not fully neutralized, degrade and embrittle RO membranes. Over time, if chemicals reach the membranes, the chemistry of these membranes changes, allowing increased salt passage. Acids and metal ions can also damage membrane materials if not controlled.
Biofouling
Bacteria and other microbes in the feed water can colonize on membrane surfaces, forming biofilm layers that are difficult to remove. Biofouling accelerates organic fouling rates.
Fouling, scaling, and chemical degradation are just a few of the challenges that RO systems can meet without proper pre-treatment. Without mitigation, these challenges increase membrane cleaning frequency, replacement costs, and unscheduled downtime. More frequent cleanings, in response to these concerns, accelerate membrane wear and degradation as well. The end result is substantially higher operating costs over the membrane lifespan. Once a system is designed improperly for the water quality present, it is very difficult to solve the problem operationally. As our RO system expert Tony Murphy emphasizes, “If you’re at that point where you have to clean your membranes every three to six months, it is important to diagnose if this is a design or operational issue. RO systems need to work for you, and too frequent of physical cleaning means this system is not operating for the purpose it was built.”
Role of Pre-Treatment
In industrial RO systems, pre-treatment refers to upstream processes that condition the feed water before it enters the membranes. The goal of pre-treatment is to remove contaminants, condition the water, that can foul or damage the RO membranes. Effective pre-treatment optimizes separation efficiency and maximizes the operational lifespan of the membrane system.
There are several key objectives for RO pre-treatment:
Protect Membranes from Fouling and Scaling
Proper pre-treatment can remove the particulate matter, colloids, iron, silica, and hardness minerals that foul or scale membranes. This reduces cleaning requirements and maintains steady flux rates.
Enhance Efficiency and Longevity
Properly pre-treated water enables the RO unit to achieve the designed product water capacity and recovery rate consistently throughout membrane life. This minimizes loss of production and reduces the frequency of costly membrane replacements. Tony shares, “Some systems, when properly designed and operated, go three, four years before needing cleaning with proper pre-treatment. This is money back in our client’s pocket.”
Ensure Consistent Water Quality
By reducing particulate matter and controlling biological growth, pre-treatment provides a consistent feed water composition for the RO unit. This enables reliable and high quality permeate production.
In addition to protecting the membranes themselves, proper pre-treatment is critical for reducing operating costs, improving uptime, and extending the service life of RO systems.
Key Aspects of Pre-Treatment
There are several important components of an effective RO pre-treatment system:
Filtration
Filtration removes suspended solids and particulates that can foul membranes. Typical filtration systems used include multi-media filters, bag filters, cartridge filters, and sometimes ultrafiltration systems. These generally remove particles down to 1-5 microns in size. The filtration process helps minimize particulate fouling of the RO unit.
Softening
Water softening reduces scaling potential by removing hardness ions like calcium, magnesium, and barium. Softening lowers the Langelier Saturation Index (LSI) to control calcium carbonate scale formation.
Activated Carbon
Activated carbon filters help remove organics, chlorine, and trace hydrocarbons ahead of the RO feed. As Tony points out, “Chlorine will severely damage the membranes – cleaning is no longer an option and you will have to replace them.” Preventing residual chlorine exposure maximizes membrane life.
Chemical Injection
Antiscalant injection prevents mineral scale formation on RO membranes. With higher water recovery rates (LINK TO RECOVERY ARITCLE HERE ONCE PUBLISHED), scaling tendency increases without proper antiscalant dosing. Projection software models determine the optimum chemical addition.
Used either independently or collectively, these pre-treatment processes maximize RO performance. They mitigate the key factors that contribute to membrane fouling and scaling while enhancing product water quality.
Choosing the Right Pre-Treatment Solutions
Selecting the appropriate combination of pre-treatment processes is crucial for any RO system. There are several important guidelines for choosing customized pre-treatment:
- Water Analysis: Comprehensive feed water testing provides key data on particulates, organics, inorganics, and microbiological content. This informs targeted fouling and scaling control. Tony emphasizes, “First question I ask a potential client looking for a quote is, have you done a water analysis? That’s number one. Without that analysis, we can’t design a system that will work for you long-term.”
- Silt Density Index: Measurement of the silt density index indicates the fouling tendency of suspended solids. A high silt density index makes additional filtration necessary.
- Flux Rate Analysis: Projected flux rates dictate the number of membranes and array configuration to manage fouling potential. Modeling software is used to optimize flux rates.
- Proprietary Software: Advanced chemistry models like those from Avista or ROSA predict scaling potential for a given water composition. This tailors the type and dosage of antiscalant required.
For large systems, a combination of multimedia filtration, ultrafiltration, softening, and chemical treatment may be warranted depending on feed water quality and pre-treatment objectives. Pilot testing helps qualify pre-treatment selection specific to the RO application. The end goal is to apply the necessary pre-treatment to curb fouling and scaling. This avoids over-engineering that drives up capital and operating expenses.
Adequate pre-treatment is fundamental to reverse osmosis system productivity, efficiency, and membrane longevity. By removing particulates, organics, bacteria, hardness ions, and other contaminants, pre-treatment minimizes fouling and scaling tendencies within the RO unit. This enables sustained flux rates, reduced frequency of cleanings, lower replacement costs, and significant cost savings over time.
While capital investment for an optimized pre-treatment system may be higher initially, the dividend is reliable operation and minimal maintenance requirements of the RO asset over its lifetime. Pre-treatment is the first line of defense to curb particulate fouling, biofouling, organic fouling, and scale formation that rapidly deteriorates membrane performance.
If you need help analyzing your water quality and designing a pre-treatment system for your facility, the experts at EAI are here to help. Reach out to us here.